
PLASTIC MATERIALS
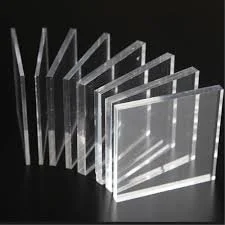
EXTRUDED ACRYLIC costs less than cast and is more dimensionally stable, meaning the thickness is more consistent across sheets. Softer, with a lower melting temperature than in its cast form, extruded acrylic is easier to laser cut, rout, and polishes more cost-effectively.

EXTRUDED POLYCARBONATE is known for its high impact strength, clarity, and temperature resistance, making it suitable for a wide range of applications. PC finds usage in a host of markets, notably in the automotive, glazing, electronic, business machine, optical media, medical, lighting and appliance markets
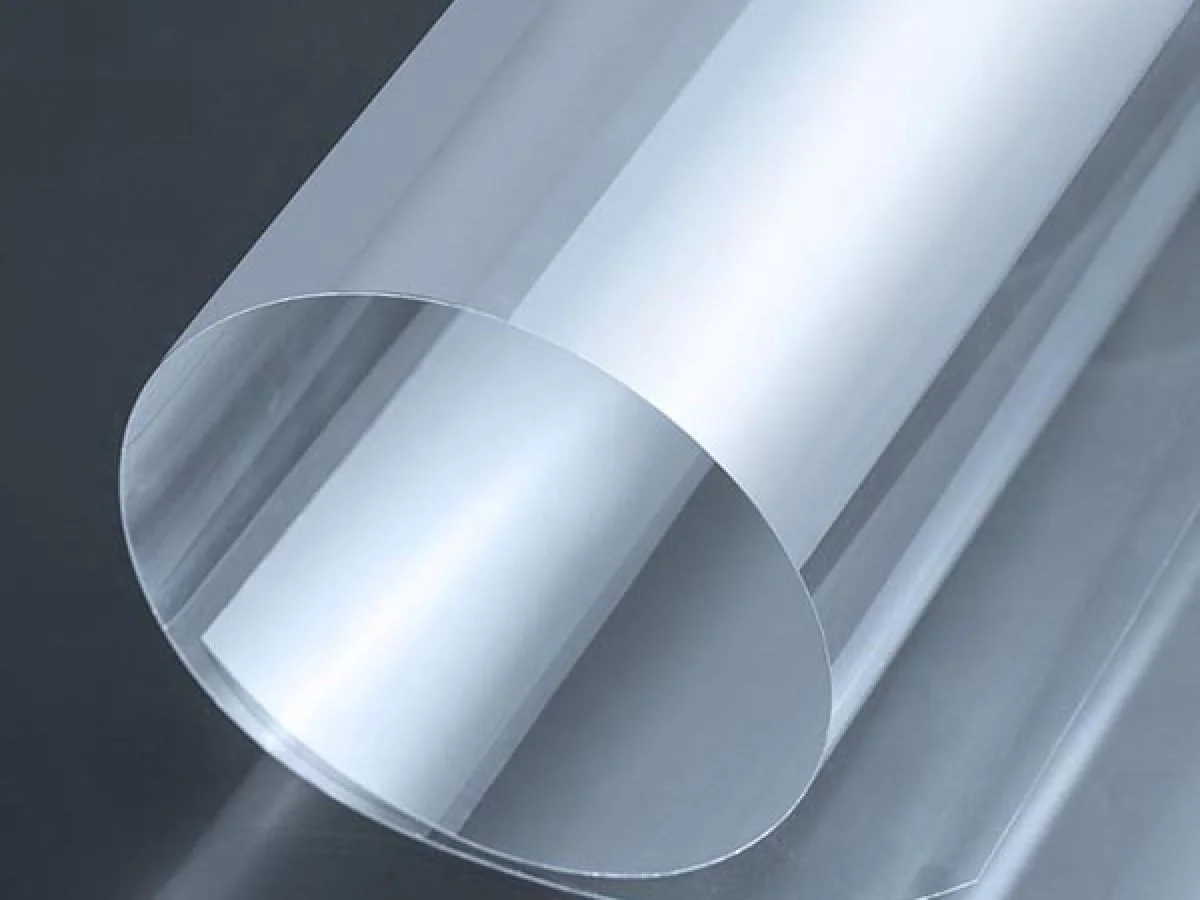
PETG is a thermoplastic polyester that provides significant chemical resistance, durability, and excellent formability for manufacturing. PETG can be easily vacuumed and pressure-formed as well as heat-bent thanks to its low forming temperatures. It is popular for consumer and commercial applications that involve 3D printing, or other heat-forming manufacturing techniques. PETG is well-suited for fabrication techniques like die cutting, routing, and bending.
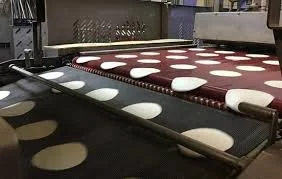
PTFE BELTS are conveyor belts made from a fiberglass or other fabric base material coated with polytetrafluoroethylene (PTFE), a synthetic polymer known for its non-stick, high-temperature resistance, and chemical inertness. They are widely used in various industries, including food processing, textile manufacturing, and electronics, due to their unique properties.
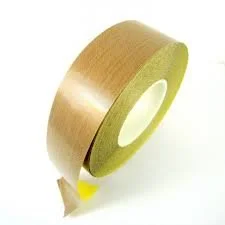
PTFE TAPE on conveyor belts provides a non-stick, high-temperature resistant surface, crucial for various industrial applications. It's often used in heat sealing, packaging, and food processing, preventing materials from sticking to the belt or equipment. This tape typically consists of a PTFE (Polytetrafluoroethylene)-coated fiberglass fabric with a high-temperature adhesive, such as silicone
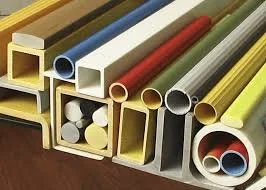
FRP PULTRUSIONS is a manufacturing process for producing continuous lengths of fiber-reinforced polymer (FRP) profiles with a constant cross-section. It involves pulling fiber reinforcements, like fiberglass, through a heated die after they are saturated with resin, resulting in a cured, structural composite part.
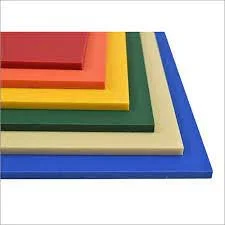
HDPE is known for its strength, durability, and resistance to moisture and chemicals, making it a widely used material in various applications, from packaging to construction
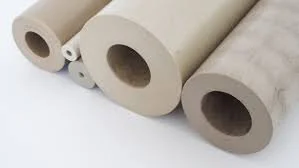
INJECTION MOLDED PEEK TUBES are manufactured by injecting molten PEEK (Polyetheretherketone) polymer into a mold cavity, where it solidifies and takes the shape of the tube. PEEK is a high-performance thermoplastic known for its excellent mechanical, chemical, and thermal properties, making it suitable for demanding applications. Injection molding allows for the mass production of PEEK tubes with high precision and repeatability.